Experts love to dissect the topic of which wheel is better – Steel or Aluminium. They can be heard citing the various differences between the two metals, the advantages and disadvantages of each, right down to their respective manufacturing processes and performance out in the field.
The weight difference, of course, is the most obvious one. For example: the Alcoa Ultra ONE® 22.5” x 8.25” wheel weighs in at just 18kg vs an equivalent steel wheel at 28-37kg, and if you put that into a Payload Calculator you’ve looking at some pretty interesting numbers!
Another strong argument for aluminium wheels is in the lowered maintenance costs they bring to the table.
The impact of choosing steel over aluminium on maintenance expenditure, such as cost of refurbishing wheels, repairing damage, and replacing tyres and brakes prematurely is an important consideration when assessing ROI over the lifetime of heavy-duty equipment.
Wheel-offs cost businesses in time that trucks are off the road and not hauling loads, they cost in repair shop charges, and they cost in employee wages that could be paid towards more productive income-generating endeavours.
Here are 4 categories of maintenance benefits that Alcoa Wheels take the prize in over steel wheels:
1. Refurbishing
Because steel wheels generally require continuous refurbishing, such as removing rust, re-painting, touching up or other labour-intensive steps, many fleets need to include refinishing of steel wheels as part of their regular truck maintenance schedule.
Aluminium wheels, on the other hand, come up like new with a simple polish and, depending on the finish of the wheel, sometimes no polish at all.
The savings in workshop labour costs are increased by removing the need to purchase paint, rust remover, or to outlay large sums for powder-coating and its ongoing maintenance.
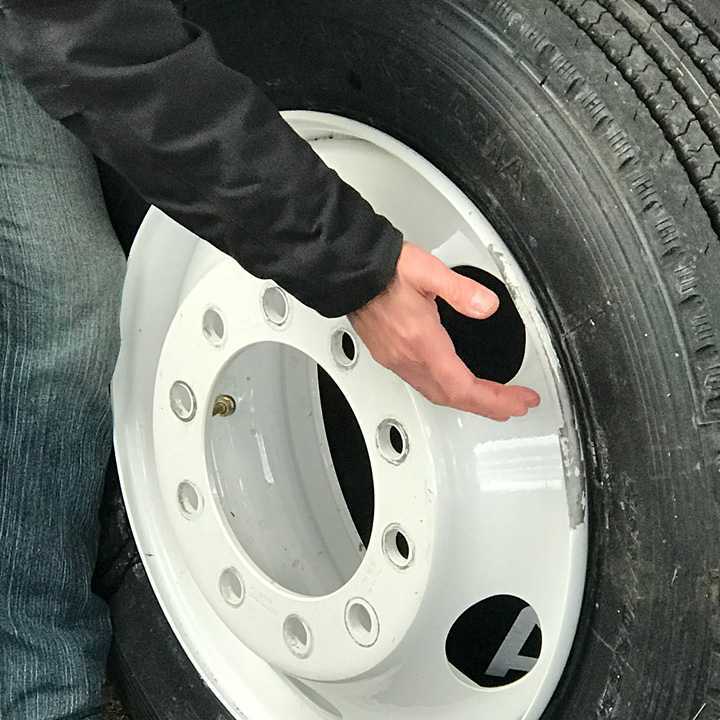
Because aluminium wheels are not painted like steel wheels, the cost savings recuperated from eliminating the need for spray paint and touch up are favourable.
“Every year equipment managers who are working with steel wheels in harsh environments have to dismount tyres, paint or touch up and then remount tyres in order to avoid the common rusty appearance found on many steel wheels,” says Ross Simmons, Managing Director for Howmet Wheel Systems, distributor of Alcoa Wheels in Australia.
2. Weathering Harsh Environments
By their very nature, truck and trailer wheels spend their entire lives exposed to the elements, and in many cases in Australia, in harsh and even hostile environments.
Steel wheels are well-known for flaking, chipping, or corrosion issues that the salt, road grime, and other outdoor elements can cause with each rotation of a wheel. The debris on the road and gravel on country and outback roads may also create damage that requires repairing.
Technologies today have advanced from liquid painting of steel wheels to powder coating that creates a non-porous surface that shields the wheels so there’s less overall damage from truck wheels being exposed in harsh environments than previously experienced.
Aluminium is durable from the start if properly maintained (thus without needing to be powder-coated), and now Alcoa Dura-Bright® Wheels take things to the next level.
The difference between Dura-Bright® Wheels and a conventional wheel coating is that Alcoa Wheels have engineered a surface treatment that penetrates the metal to form one composite – becoming one with the aluminium and increasing its resistance to corrosion by 10 times their previous Dura-Bright® range.
Dura-Bright® Wheels’ low surface energy and large contact angle mean that less dirt adheres to the wheel.
And, the best part is that they clean up with just soap and water. In Japanese tests, wheel wash time was reduced from 25 minutes to just 2!
These easy-to-clean benefits help to lower lifetime operating costs.
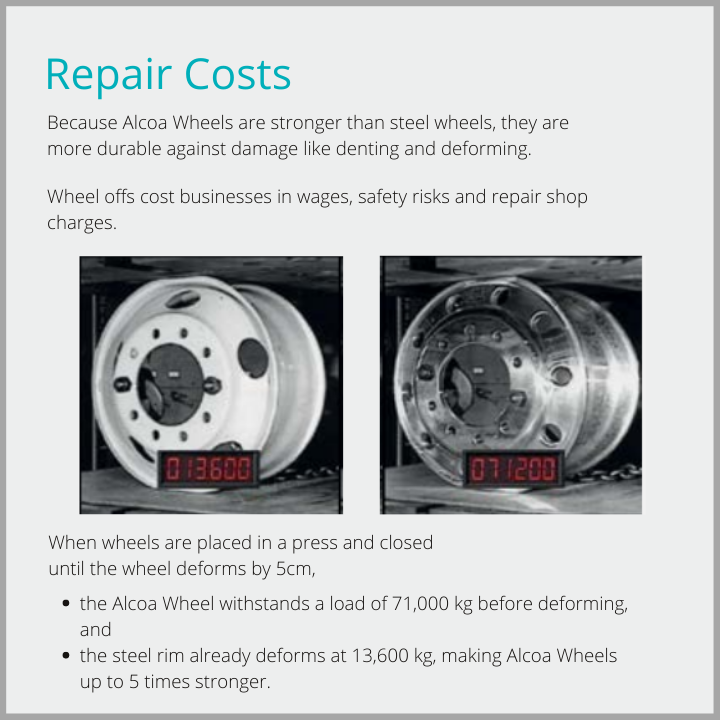
3. Strength
Did you know that a one-piece forged aluminium wheel is up to 5 times stronger than an equivalent steel wheel?
It’s been tested. In internal strength tests, when wheels are placed in a press and closed until the wheel deforms by 5cm, the Alcoa Wheel withstands a load of 71,000 kg before deforming, and the steel rim already deforms at 13,600 kg.
A wheel that is durable enough not to buckle and dent prevents costly wheel-offs and repair charges, not to mention reducing the number employees are exposed to safety risks of frequent wheel changes.
For example: Wheel changes 4 times a year due to damage compared to only once a year means you’ve 3 reduced your associated risk and costs by 3 times.
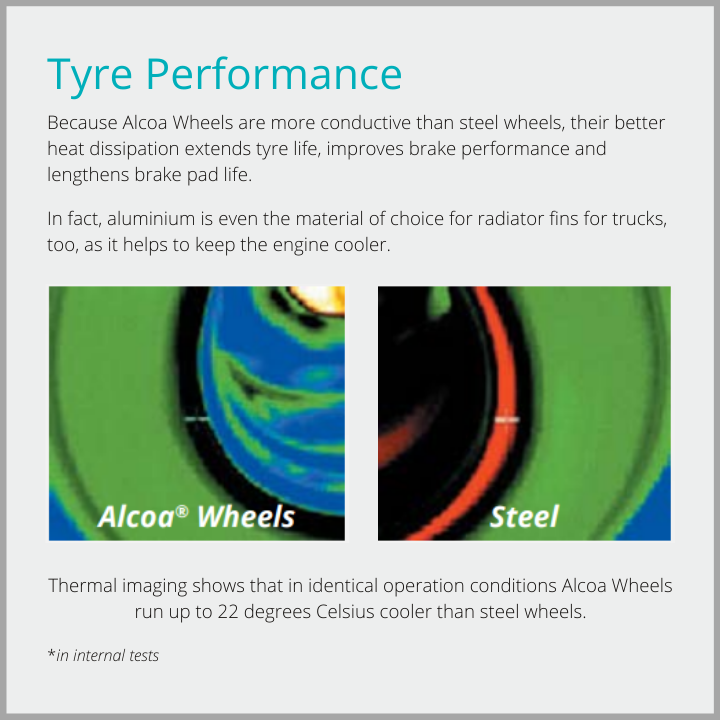
4. Heat Dissipation
Improved heat dissipation contributes to longer tyre and brake life and it’s a fact that aluminium dissipates heat better than steel – 15 times faster in fact!
As an important aside: in a heat event like a brake related incident, it is important to understand the impact the heat has on the wheel. An overheated wheel must be removed from service immediately. Learn more about the warning signs your wheels have overheated and how the Heat Indicator on your Alcoa Wheels works.
In Queensland, Brisbane City Council has seen the cost benefits of tyre life being extended and lowered break issues after fitting their buses with Alcoa forged aluminium wheels instead of steel wheels.
If we look at an inner city bus that stops-and-goes hundreds of times in a day, often in already high temperatures in the warmer parts of Australia, the benefit of aluminium giving up heat faster is key to taking heat away from the brakes thus keeping tyres from wearing out.
Because steel holds onto the heat, that heat continues to rise even after parking the bus. Aluminium wheels, on the other hand, help to quickly cool down the system and prevent heat damage to the brakes and tyres.
Longer brake and tyre life converts to dollars saved when they are replaced less often.
Listen to Alcoa wheel experts Doug Mason, Mike Yagely and Dave Walters talk about the age old debate that is Aluminium Wheels vs Steel Wheels over on the Behind the Wheels Podcast.
Make Sure It’s An Alcoa® Wheel
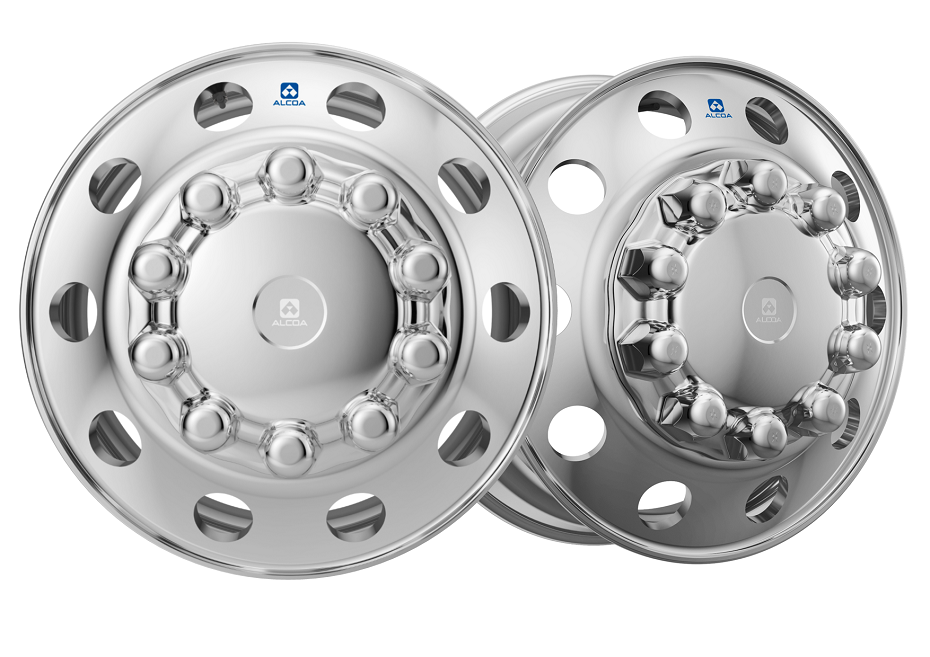
To spec your wheels, ring 1800 955 191 to talk with our wheel experts, or fill out a contact form and we will reach out to you to answer your questions and discuss your specifications.