Proprietary Treatment Keeps Wheels Shiny and Corrosion Free with Less Maintenance
Your trucks spend a lot of time on the road. Don’t let the road spend a lot of time on your trucks.
Outside of the comfort of their terminal or garage, there are road salts, deicers and other chemicals, and road debris that all make for a harsh, corrosive environment just waiting to attack your trucks and their wheels mile after mile. There can also be acid in truck washes, which can further add to the damage.
Winter months are especially bad for your equipment. Navigating tough terrains and challenging conditions means fleets need reliable wheels that provide protection from any environment to keep them lasting longer and looking their best.
Steel wheels can easily rust, even when coated. Aluminum wheels typically have to be polished to keep them shiny. Over time, an oxide starts building up and it gets thicker, and the wheel becomes duller and duller. Polishing, which requires a decent amount of effort, removes the outside oxide layer to bring back the bright shine of the raw aluminum.
Conventional coatings can be used to protect the aluminum underneath, but they essentially lie on top of the surface without actually bonding to it. Using an acrylic clear coating as an example of one of these conventional coatings, it sits on top of the aluminum. Eventually, corrosion can get underneath the coating and can continue to spread. This is called filiform corrosion and it looks almost like snowflakes forming. If the surface of an acrylic clear coat is scratched, corrosion will grow underneath the coating.
A Different Kind of Protection
An alternative to conventional coatings is a surface treatment that interfaces with the base aluminum to form a molecular bond, in essence becoming part of the wheel itself. That was the goal scientists at Alcoa® Wheels had when they set out to develop a new type of treatment, which led to the creation of Alcoa® Dura-Bright® Surface Treatment and the advent of Alcoa® Dura-Bright® Wheels.
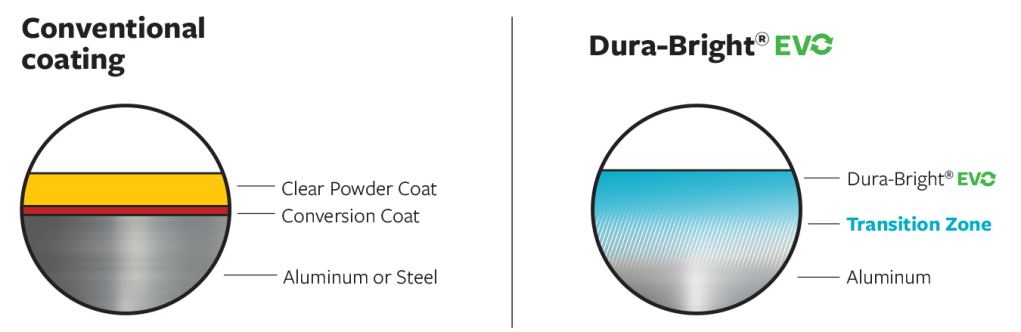
The proprietary Dura-Bright® Surface Treatment on the wheels is engineered to endure the harshest conditions, combating corrosion, and maintaining a shiny, brand-new look with minimal maintenance. The Dura-Bright® Surface Treatment forms a molecular bond with the wheel, meaning it won’t crack, peel, or corrode like coated wheels, keeping it looking newer for longer without polishing or painting or time-consuming cleaning. Dura-Bright® Wheels utilizes technology that’s been tested and proven in harsh conditions throughout the years.
The Science on the Surface
From a scientific perspective, the surface treatment is a breakthrough because it provides a wheel with very low surface tension where there are intermolecular forces that repel water, dirt, and chemicals. It essentially creates a barrier around the wheel to ensure they remain shiny and corrosion-free regardless of the road conditions. The lower the surface tension, the less likely dirt will stick.
A water droplet is a good indication of surface tension, which is measured by the angle water droplets bead up. An untreated polished aluminum wheel has a medium contact angle and water droplets flatten out slightly with some puddling, indicating a medium surface tension. A painted steel wheel has a lower contact angle, indicating a higher surface tension. It allows water to flatten out and puddle, and dirt to stick.
In testing, water droplets on the painted steel wheel slowly roll off while water droplets on the Dura-Bright® Wheel roll quickly off and leave nothing behind. That’s because Dura-Bright® Wheels have a larger contact angle, indicating a lower surface tension, which keeps water beading and dirt from sticking.
Easier Cleaning with Just Soap and Water
Because the Dura-Bright® production process penetrates the aluminum, the surface treatment ensures that wheels not only shine bright but stay that way even after hundreds of washes and thousands of miles without polishing.
Dura-Bright® Wheels can be easily cleaned with mild soap and water, eliminating the need for harsh cleaning products, further protecting the environment, and reducing maintenance costs and downtime. The first cleaning step is a water pre-rinse followed by applying the soap or detergent using a spray applicator, a soft-bristled brush or soft sponge, and then finally a clean water rinse.
How to Specify Dura-Bright® Surface Treatment
Product specification begins with answering some basic questions, such as number of bolt holes, bolt circle diameter, hub bore, wheel sizes, and more. After those questions are answered, additional options – like the Dura-Bright® Surface Treatment – can be chosen.
In the Dura-Bright® column in the spec guide, there are four options: 0DB, 1DB, 2DB, and 3DB. These combinations are added to the part number when ordering a wheel. As an example, to order the ULA18x wheel with mirror polish on both sides with Dura-Bright® Surface Treatment, the final part number would be ULA183DB. In the spec guide, DB stands for Dura Bright.
- 0DB – stands for brush finish with Dura-Bright® to cover both sides of the wheel.
- 1DB – stands for mirror polish with Dura-Bright® to cover the first position of the wheel–face.
- 2DB – stands for mirror polish with Dura-Bright® to cover the second position – inside of the wheel.
- 3DB – stands for mirror polish with Dura-Bright® to cover both sides of the wheel.
Learn more about how Alcoa® Dura-Bright® Wheels are engineered to outlast and outshine, and how you can save time and money by keeping your trucks on the road more and looking their best with a lot less effort.